Retailers and Their Issues with Logistics
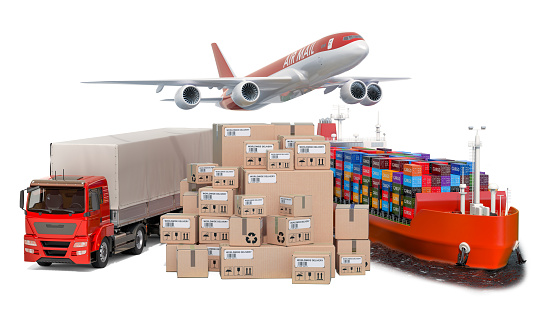
Retailers are always striving for excellence in logistics due to limited trade margins. As a result, improving the efficiency of product delivery from the distribution center (DC) to retailers is a continuous endeavor in retailing. For refilling store goods from warehouses, retailers must develop appropriate delivery rules and optimize truck routes.
The majority of retail shops follow predictable weekly demand trends. As a result, grocers adapt to consumer and store demand by offering retailers with store-specific delivery patterns on a cyclical basis. A delivery pattern is a set of weekdays on which a delivery from the DC arrives to a certain shop on a regular basis during all standard weeks in a planning horizon, that is, weeks without public holidays. Empirical studies show that the vast majority of grocery stores use similar delivery patterns, which are often based on sales volume and shop size.
There are numerous advantages to using repeated and store-specific delivery patterns. Because order replenishments arrive at a shop on the same weekdays each week, scheduling the personnel for the shelf replenishment procedure is considerably easier. Similarly, in terms of transportation, delivery patterns allow for the creation of fundamental cycle routes during each planning period.
Staff deployment and shift planning at the DC may be changed based on projected aggregate picking volumes, which are determined by delivery patterns chosen across all shops. And most shops have procedures in place that require them to evaluate their inventory on a regular basis. A replenishment order is sent whenever shelf inventory falls to or below a reorder level. Using a cyclic ordering and delivery strategy allows for regular adjustments to reorder levels, which reduces overhead steering and simplifies logistics planning in later planning modules.
As a result, the delivery patterns chosen have a significant impact on the efficiency of the internal retail supply chain's operational subsystems, such as DC, transportation, and in-store logistics. Because order intervals are determined by the delivery pattern used, volume effects arise across the supply chain, which have a significant impact on logistics costs. Due to the difficulty of building up relevant models and tools, most retailers do not yet employ integrative techniques across all subsystems when assigning delivery patterns to shops. For retail firms to make "optimal" or "near-optimal" decisions, proper decision support is required.
Track & Trace Your Post Tracking Number
Input the post tracking number issued to your item in the input form if you'd like to check where your product is. If you want home delivery or transportation, the vendor or supplier should issue you with this post tracking number. In the menu bar, you can also choose your parcel delivery service.
Third-party providers, such as courier service companies, have become an increasingly essential and critical factor in allowing seamless movement of items across the supply chain network as a result of the fast rise of online purchasing. Courier service businesses, on the other hand, experienced operational problems as they tried to keep up with the ever-increasing demand from the e-commerce industry, all while ensuring client happiness.
Admin